Could a fatal accident happen at your facility?
The Occupational Safety and Health Administration (OSHA) passed the Process Safety Management (PSM) standard in 1992, in response to several fatal accidents involving the release of highly hazardous chemicals, with the intention of eliminating or minimizing the potential for such events. Yet, more than 25 years later, we still see serious accidents related to these highly hazardous chemicals, with a fire and explosion involving PSM-regulated materials in Philadelphia just this summer.
Partially in response to the number of fatal accidents and catastrophic releases occurring at PSM-regulated facilities, in 2017 OSHA updated one of its National Emphasis Programs (NEPs, temporary programs that focus OSHA's resources on particular hazards and high-hazard industries) to merge all PSM-regulated facilities under one umbrella (whereas previously the chemical and petroleum industries had been addressed under separate NEPs). The 2017 NEP includes new inspection techniques designed to verify full implementation of the PSM standard.
One can expect this will lead to more inspections—and more enforcement actions. OSHA will use several sources in identifying targets for inspections, including facilities that have submitted Risk Management Plans (RMP), facilities with prior PSM violations, and local OSHA office knowledge. Accidents or complaints may also trigger OSHA PSM inspections.
We continue to see facilities face challenges when ensuring they have a robust PSM program that not only provides a safe work environment and minimizes the chances they could experience a fatal PSM accident, but also that they meet all of OSHA requirements in this heightened regulatory climate. Below we can see trends in the top citations issued by OSHA under the PSM Standard, both before and after the 2017 NEP.
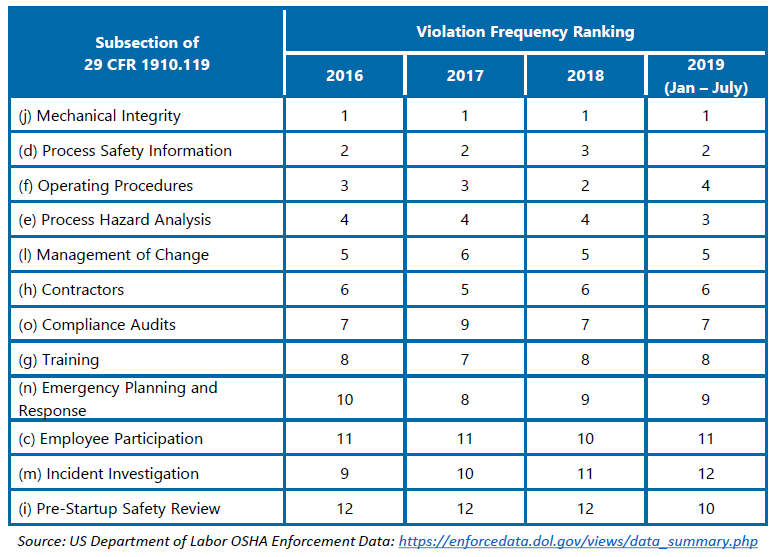
As you can see, mechanical integrity has remained the top category of citations. Operating procedures and having adequate process safety information on all PSM units and the maximum intended inventories of chemicals has been closely ranked as second and third, with process hazard analysis a tight fourth. Trends for 2019 so far show that process hazard analysis is moving up in the ranks.
How prepared are you for an OSHA inspection?
In the 2017 NEP, OSHA provided high level guidance on how they will conduct inspections of PSM facilities going forward. Of note is that they will be using a dynamic list of audit questions that will not be publicly disclosed. Facilities that are targeted for audits can expect that OSHA will review a certain set of documents before and during their inspection. Here are some highlights of what you can expect:
OSHA will then perform physical inspections of selected units using human inspectors or possibly an unmanned aircraft system (or drone) and interviews with operators, supervisors and contractors to verify that the written PSM program elements are being fully implemented at the facility. These clarified and expanded inspection elements under the 2017 NEP are intended to ensure the OSHA inspectors dig deeper than paperwork reviews and look for evidence that the PSM processes and units are actually following the PSM regulatory requirements, so that future accidents can be avoided.
By having a PSM program in place that is truly designed to prevent a catastrophe, not only will you have the programs and records listed above in order, but you’ll also have a program that will easily pass an OSHA inspection.
The Chemical Safety Board (CSB) provides well-researched recommendations
The CSB, a federal agency that investigates chemical accidents, looks at root causes of the significant— often fatal —accidents involving highly hazardous accidents. The CSB’s goal is to drive change in chemical safety through recommendations to a variety of parties, including government entities, safety organizations, trade unions, trade associations, corporations, emergency response organizations, educational institutions and public interest groups. These recommendations are published in CSB investigation reports, and facility responses are monitored and evaluated by CSB staff before the CSB Board will vote to close out a recommendation.
Trends and typical recommendations for chemical manufacturers are often in line with the goals of the OSHA 2017 NEP. While the CSB does not compile its recommendations into one summary document, the most recent CSB reports (2013 – 2019) identified recommended actions such as:
- Retain qualified, independent firms to conduct engineering analyses of PSM-covered units and processes to ensure they meet industry standards regarding fitness for service and follow NFPA, API, AIChE, and/or CCPS standards as applicable. Ensure critical process equipment is safely designed and is based on sound engineering principles. Review and update safeguards for high hazard process (HHP) areas, e.g., engineering controls, construction materials, PPE, procedures, maintenance, emergency response and release detection and alarms.
- Institute preventive maintenance programs for HHP areas that have sufficient redundancy (e.g., human review of computerized systems output) in tracking and scheduling of preventive maintenance activities.
- Develop programs that ensure operating procedures are written and cover all modes of operation (e.g., normal startup, operation and shutdown; temporary operations; emergency shutdown, emergency operations; and startup following a turnaround or emergency shutdown).
- Conduct damage mechanism reviews (DMR) in conjunction with process hazard analysis (PHA) activities to cross-link these programs and effectively manage identified hazards.
- Ensure work procedures require confirmation that all safety alarms and interlocks are in proper working order prior to startup of all HHP units. Develop alarm philosophy and alarm rationalization process, and create an alarm management program to prevent nuisance alarms and other system malfunctions.
- Conduct a siting study that includes an analysis of the consequences, necessary preventive measures, and emergency planning and response programs relevant to all applicable failure scenarios.
- Evaluate potential extreme weather conditions that might occur, and establish requirements to ensure that critical safeguards, such as backup power, will function as intended during extreme weather events, including hurricanes or floods.
- Clearly detail in-plant emergency procedures and the alerting and notification protocols for different types of plant emergencies. Ensure that all facility fire brigade and emergency response team members are trained in the National Incident Management System procedures and how to assess and respond to foreseeable plant emergencies.
- Evaluate the human control-system interface, operator fatigue and control system familiarity and training and implement processes to reduce identified risks. Ensure operating procedures and checklists are understood by the operators responsible for using them, and provide training on recognizing and handling abnormal situations.
Develop and implement a management of organizational change (MOC) protocol to allow for the transfer of knowledge and information to new personnel, at a minimum including initial or refresher training in the following:
- Safety and health procedures
- Lessons learned from previous incidents
- Technical information for equipment
- Routine plant operations
Following these and other critical CSB recommendations can assist you in ensuring you have a robust PSM program that will not only guide you through an OSHA inspection, it will also help keep your employees and community safer.